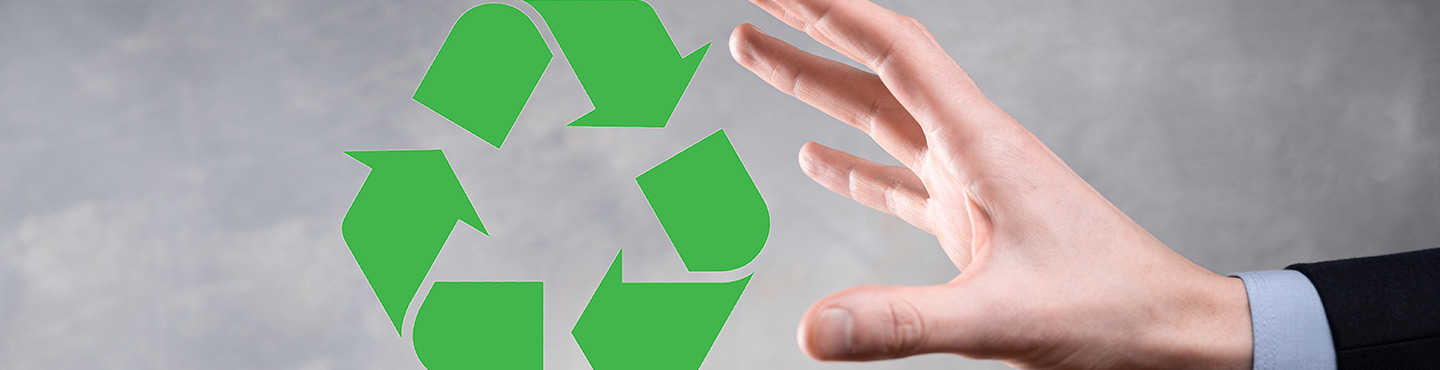
Circular economy
95% of the waste generated during the manufacturing process can be recycled or reused in its Hungarocell Green Programme the Company now collects and recycles the cuttings (EPS and XPS) of the insulation material delivered, a total of 4,000 m3.
Masterplast’s manufacturing activities generate waste, 95% of which is recycled into the production process or reused through sale. Thus, the company’s activities are less about the impact of waste generation than about waste recovery and increasing the recycling rate. In order to minimise transition waste generation, it optimises cutting widths to minimise waste production.
Recycling extrusion line – 100% recycling of clean PE foam waste into the own production process to produce a complete finished product. The company uses dedicated waste management equipment such as PE waste shredders, compactors – up to 1:50 compaction ratio – and balers, in terms of environmental awareness.
In the case of EPS, the company recovers and recycles 4,000 m3 of unused sheets. In this way, the remaining product is not landfilled as waste and does not harm the environment or human health. The recovered EPS products are not dismantled but recycled, so there is no incineration and no emissions. In 2020, the Group acquired Fidelis Bau Kft., a company engaged in the recycling of polystyrene and the production of lightweight insulating concrete. Taking advantage of the opportunity arising from this acquisition, Masterplast has launched a polystyrene recovery program in Hungary in compliance with circular economy that is unique in the building materials industry. Through its Eco-Point partner network Masterplast collects the construction residues from the polystyrene products it supplies and recycles them 100%,producing again thermal insulation material and in this way considerably reducing the amount of waste on the construction site. Non-recyclable surplus waste material generated during production is transported free of charge and recycled in their own production process to make Thermobeton.
The company intends to continuously increase the volume of EPS sheets retrieved. This is how Masterplast Group contributes to responsible consumption and production.
Cutting waste is also recycled in Masterplast Medical products, which is the starting point of the green strategy, but the Group has set much more ambitious targets. In the future, it plans to recover the single-use textiles it sells and recycle them in production after processing. By extending the ultrasonic sewing process already used in the production of disposable bed linen, it intends to make the recycling of these products even more efficient, without the use of foreign matter, by producing polypropylene granules directly after collection.
In all cases in the value chain, waste that cannot be recycled by the company’s own technology (PE, PE fleece, packaging film, paper, galvanised sheet waste) is sold for recycling.
Sárszentmihály | Masterfoam Kft. | T-Cell | Szabadka (üvegszál gyártás) | |
---|---|---|---|---|
Percentage of waste recycled from production waste | 6% | 75% | 94% | 0% |
Percentage of production waste to be disposed | 25% | 0% | 1% | 0% |
Percentage of waste sold for recovery | 69% | 25% | 5% | 100% |
CSR Hungary, The Hungarian Business Responsibility Award in 2021. Hungarocell Green Programme in the category „Best innovation for the circular economy” – More than 70 Eco-Point nationwide, 4,000 m3 of recycled material